Bridges
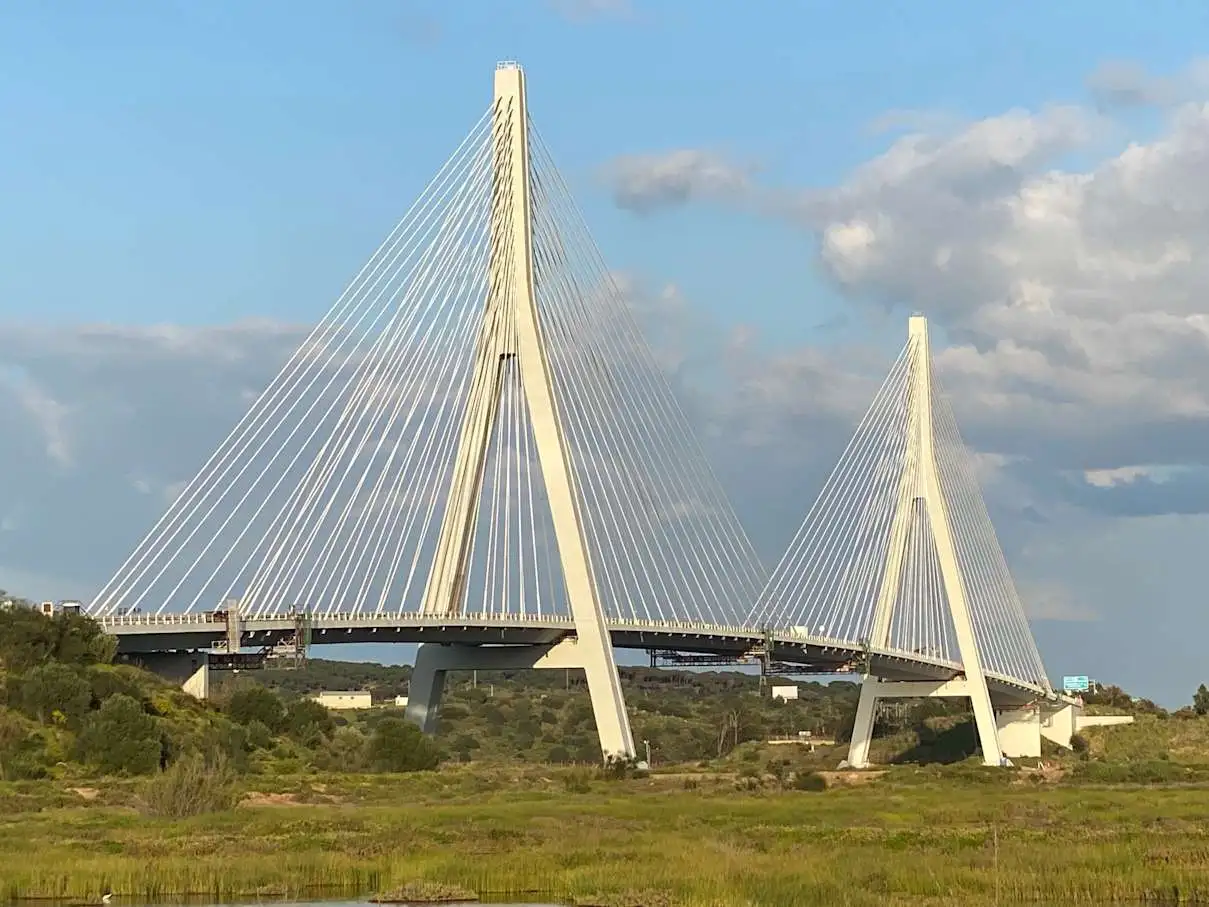
Cable supported bridges
With the increasing spans and cable lengths of cable supported bridges, efficient hydraulic dampers are required for stabilizing vibrations on the stay cables and bridge girders. In co-operation with our customers, we at Dellner Dampers customize and supply the most effective and durable hydraulic dampers to solve this problem.
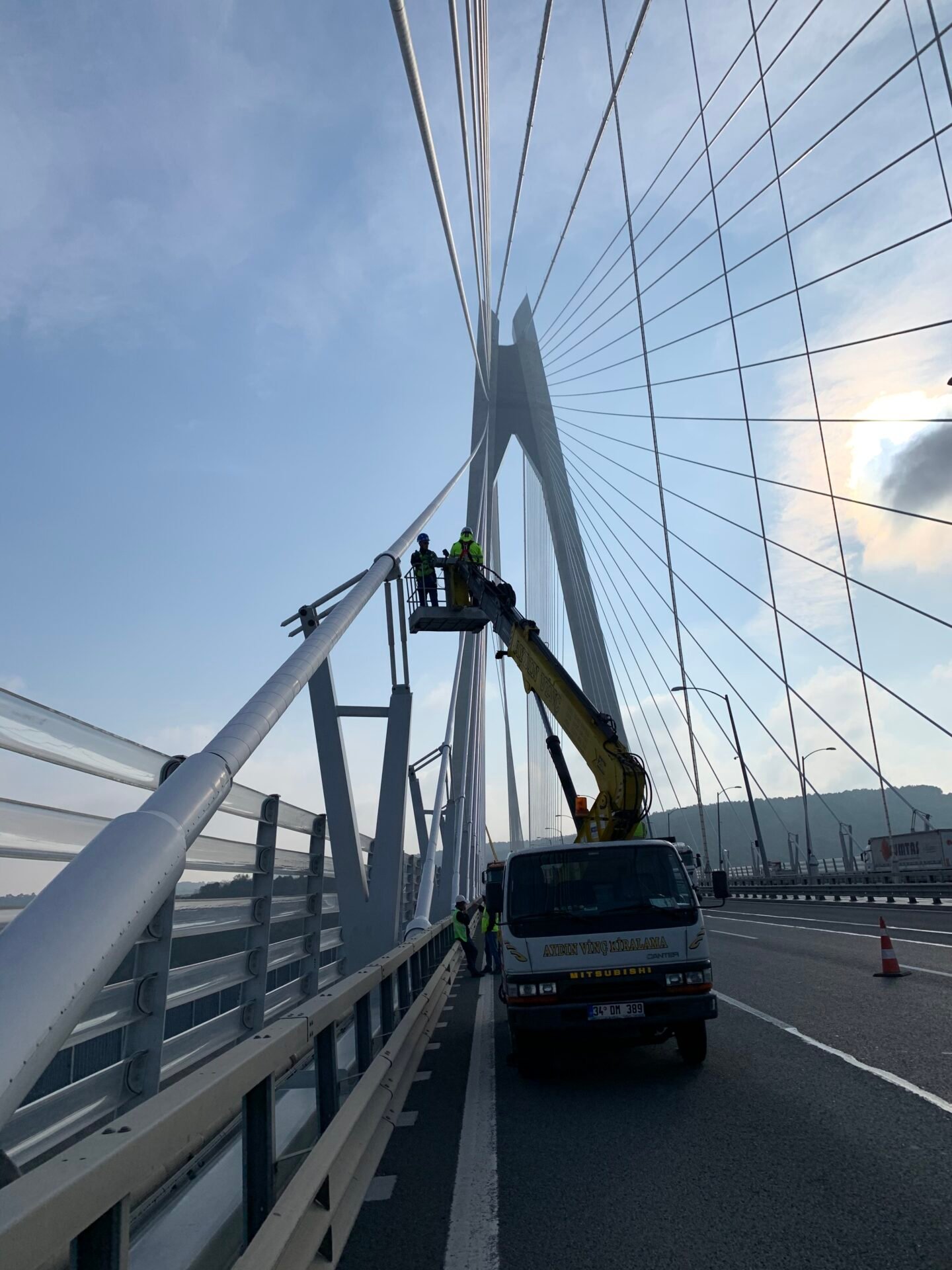
Vibration problems in cable stayed bridges
On long-span cable stayed bridges you can have the appearance of vibration problems. Those vibrations are induced by traffic load and aerodynamic effects on the stay cables cause by wind, rain, snow and ice – often in combination. These vibrations put stress on the bridge structure and reduce cable lifespan but also affect the wildlife wellness as of unwanted frequences. Our specially designed hydraulic dampers provide the perfect solution to fix this issue.
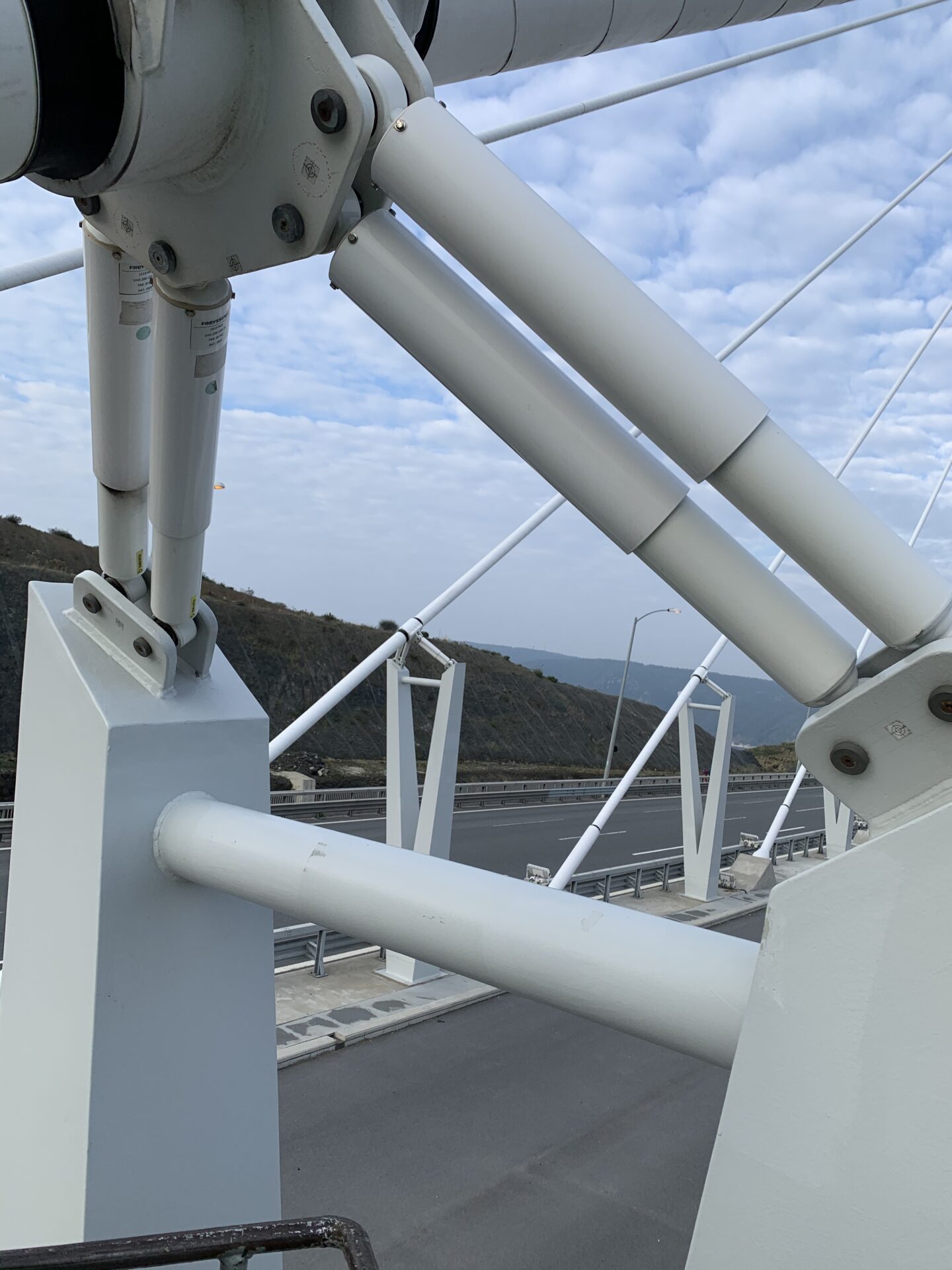
Cable dampers - Customized and individually tuned for each bridge
Equipping the stay or grinder cables with Dellner Dampers viscous dampers is the most effective way to reduce or eliminate induced vibrations. Every damper is fine tuned for each individual cable property at the specific bridge, to ensure the optimal response force. The dampers are installed close to the bridge deck and connected to the cable anchors with required interfaces in tailor made casings or connections. Depending on the needs and system used, the corrosion protection and materials used are also customized to meet each unique requirement.
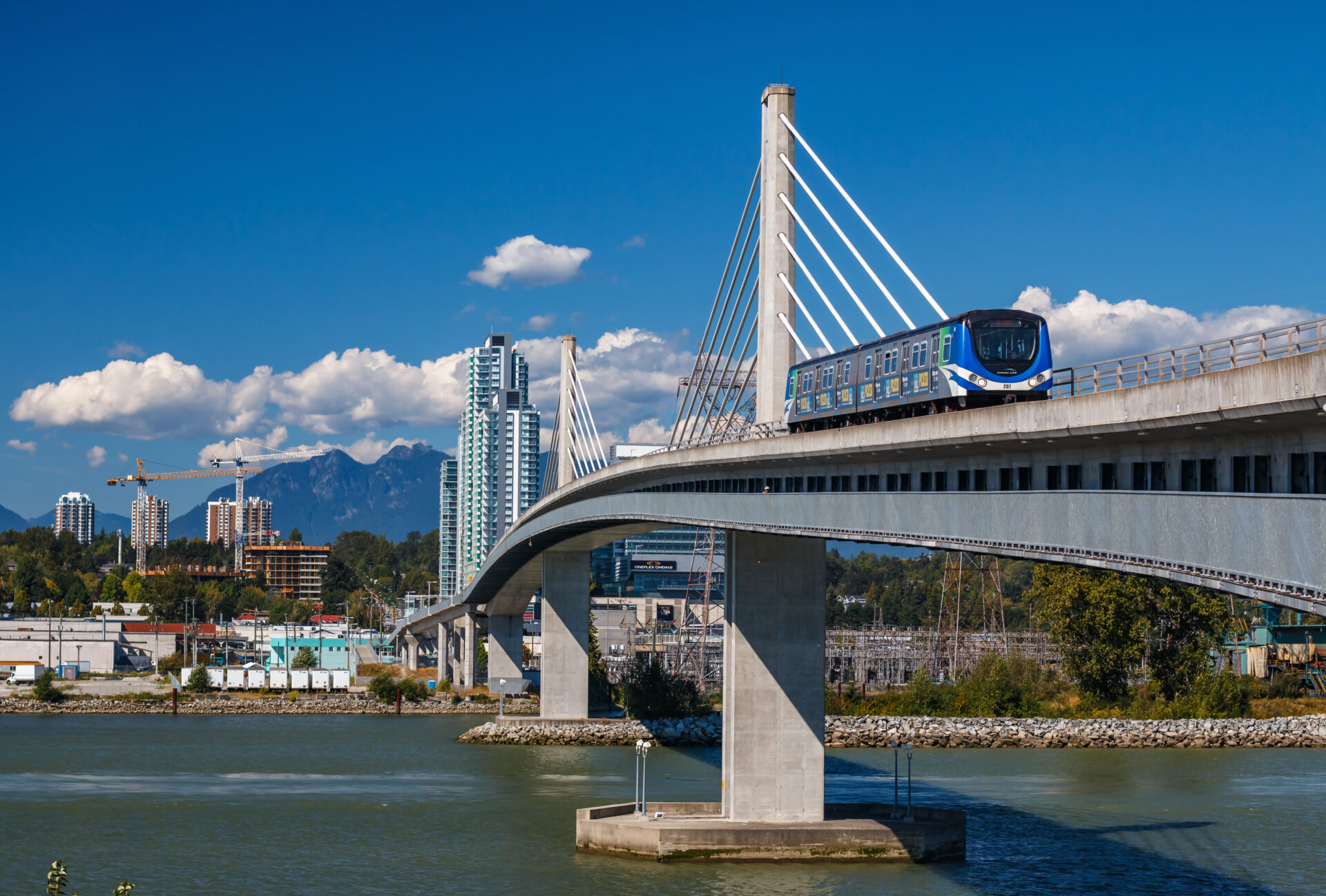
Bridge Damper Designs
Our Bridge Dampers are available in three different base designs depending on the bridge design and cable lengths. Each damper is customized for the individual cable damping characteristic needed.
- Type 45 – Fmax 20 kN
- Type 62 – Fmax 30 kN
- Type 62 Plus – Fmax 50 kN
- Type 62 Heavy Duty – Fmax 50 kN
- Type 80 – Fmax 70 kN
The damper is a twin tube hydraulic telescopic damper. The required damping force is generated by viscous losses when oil being forced through a calibrated flow restriction. The inner cylinder contains only oil while the reservoir between the housing and the cylinder contains oil and air. Both ends of the damper, the interfaces, are usually equipped with spherical bearings or pin bearings but can also be customized.

Long lasting lifetime
Our dampers have undergone rigorous fatigue, salt spray, and temperature testing to ensure durability and performance over time.
Fatigue tests have been performed at different combinations of amplitude and frequencies for millions of cycles, corresponding to damper travel distances up to 1.9 million meters. Damper characteristic tests performed before, throughout and after fatigue loads conclude no detectable degradation of the damper performance. And it is noticeable that the equilibrium temperature does not change much during the testing procedure and after visual inspection, the dampers show minimal visible or no signs of wear.
The accelerated 500 hrs salt spray test corrosion test has been performed with excellent results.
The dampers have also been operational function tested in temperatures from -40°C to + 60°C, with performance according to requirements at all intervals.
The proof of our testing are the actual durability of the +1000 dampers on +70 long-span bridges for the last +20years, all over the world and often in very corrosive environment. It says it all – Quality ensured and guaranteed, by other means.
Movable bridges
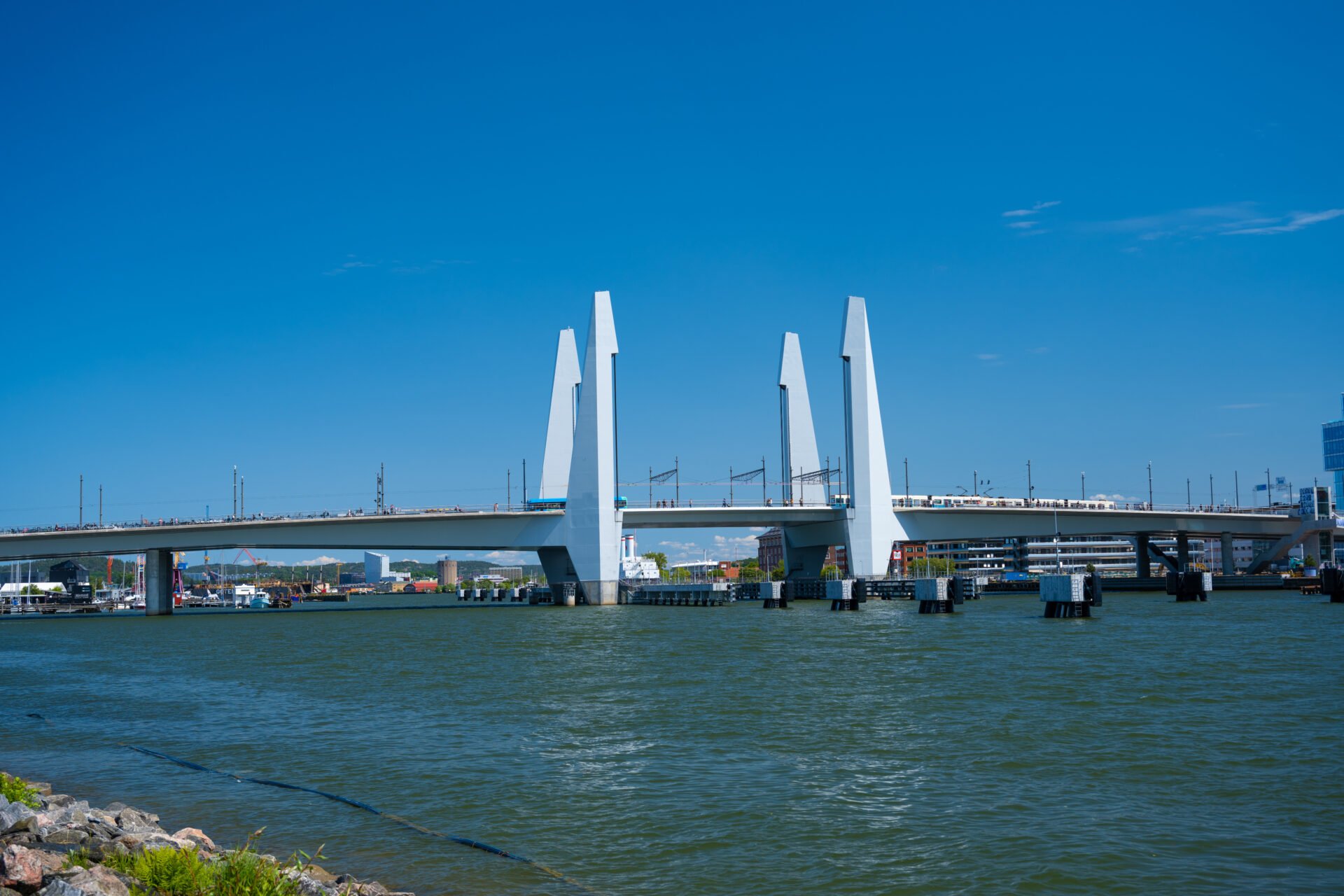
Buffers for movable bridges - Customized and individual tuned for each bridge
For movable and bascule bridges we offer our gas-hydraulic energy absorbers in the HYBUFF G-series, reducing structural impact when opening and closing of the bridge.
As bridges usually require extremely high demands on environmental protection, such as specific corrosion resistant coatings or choice of materials, we offer our buffers purposely designed and manufactured for each individual need and requirement.